Unlike many other mass-oriented flooring producers with a narrow assortment and fully automated production, all WOODlife floors are made-to-order with attention to detail. This allows the manufacturer to customize any aspect of its floors such as: thickness, length, surface structure (sanded, brushed, planed, fine sawn, distressed), bevels, filler color, and individual floor design.
WOODlife offers a vast range of dimensions in plank and numerous patterns: widths from 5 to 38 cm (2 to 15 inches), and lengths of up to 7.5 meters (25 feet).
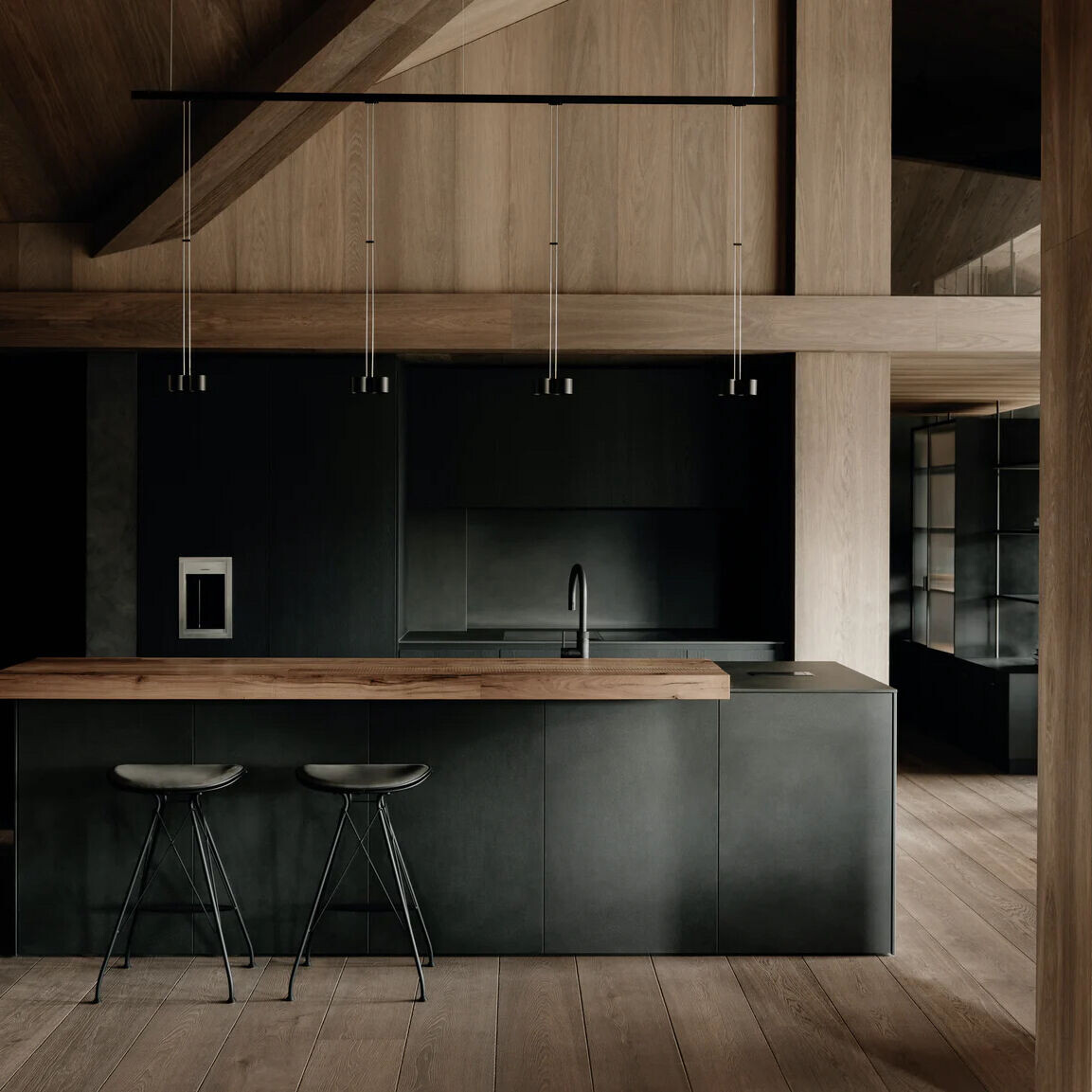
Manufacturing details
- Top layers are pressed onto the plywood, using a waterproof, high performance 2-component EPI-glue. The adhesive is ideal for gluing critical materials and species such as core smoked oak and resinous wood species such as douglas fir.
- Open defects are optimized by hand: bark and loose particles are removed to ensure a proper bonding of the filler, even after future sanding
- The color of the 2-component filler is adapted to the chosen finish
- 100% factory cured, natural hardwax finishes, which can all be upgraded to our scratch resistant, innovative Varnax® finish system.
- Cfl and even Bfl-s1 fire retardant classification according to the European fire classes (Euroclasses)
- WOODlife’s multiplanks have passed tests for all major European regulations on the presence of harmful chemical substances in wooden flooring
- Most floor types are suited for underfloor heating and cooling.
- WOODlife offers a special manual treatment that makes its floors suitable for wet areas such as toilets, bathrooms and spas.
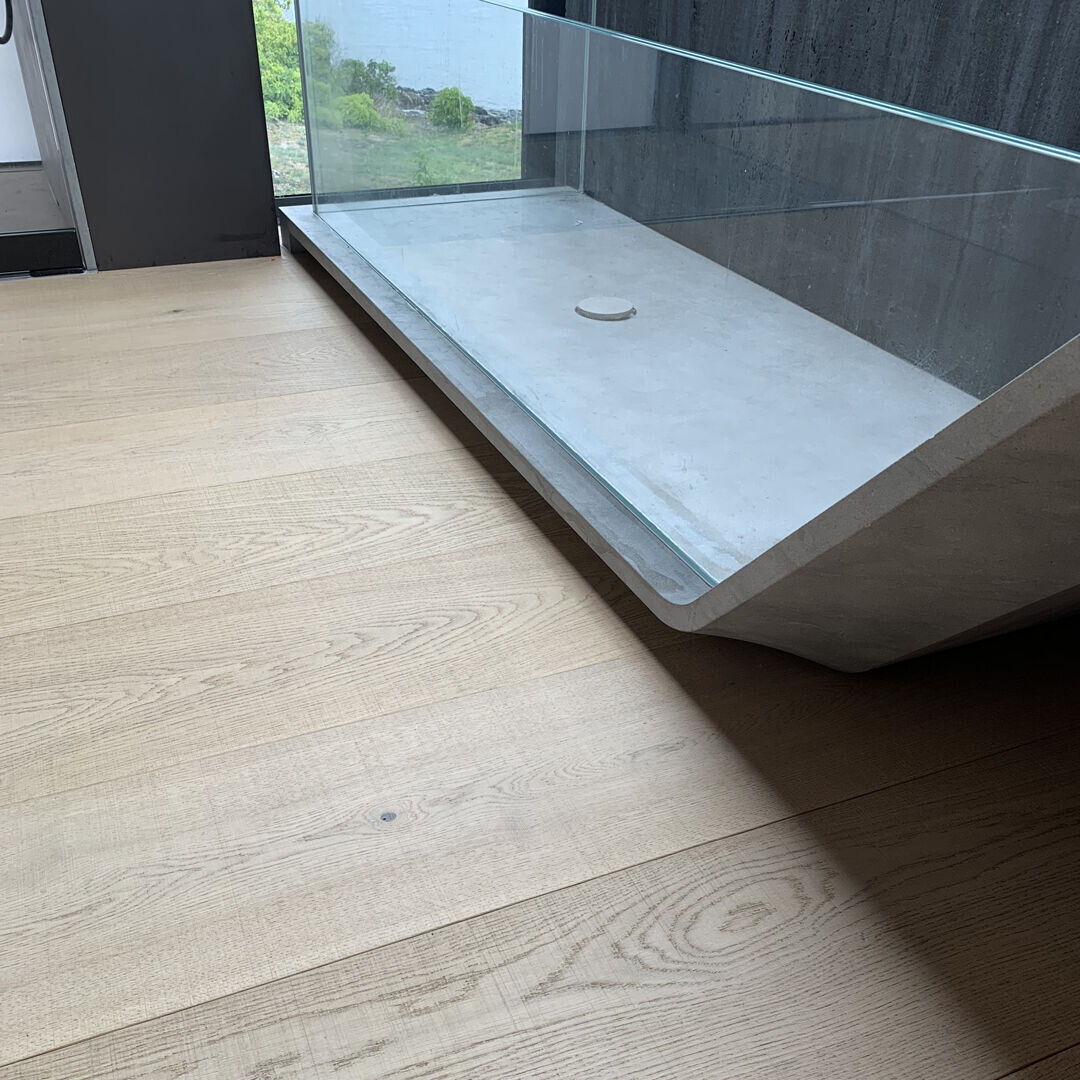
Cut when wet
WOODlife's engineered wooden floors are otherwise known as multiplanks. A multiplank typically consists of two layers. The bottom layer is made from water-resistant birch plywood on which a 4.5- or 6.5-mm top layer has been glued. These two layers combined form an exceptionally strong and reliable multiplank which will last a lifetime, even in extreme climates and over underfloor heating.
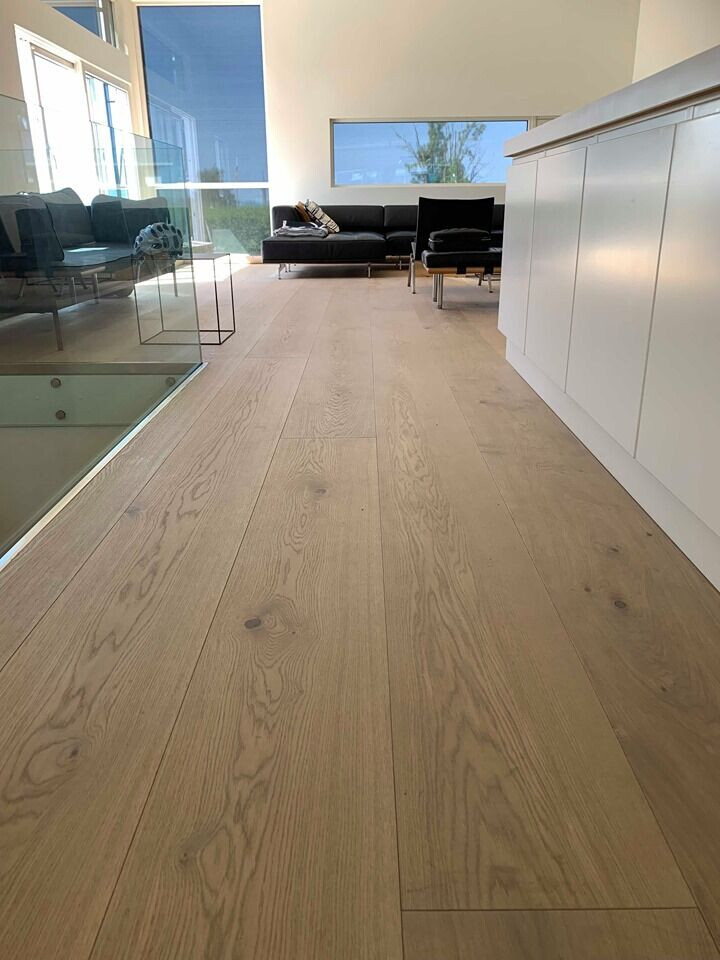
WOODlife cuts its top layers fresh from the log, one at a time, and dries the top layers afterwards at a slow pace at modest temperatures. This is rather unusual; the vast majority of producers cut their top layers from dried oak wood. By going the extra mile, the artisanal approach provides us essential advantages:
- no hidden tension and hair cracks: hair cracks often lead to larger cracks in more extreme climatic circumstances and on underfloor heating.
- no unnatural discoloration: especially in the cleaner grades, our floors show a more natural and uniform color palette.
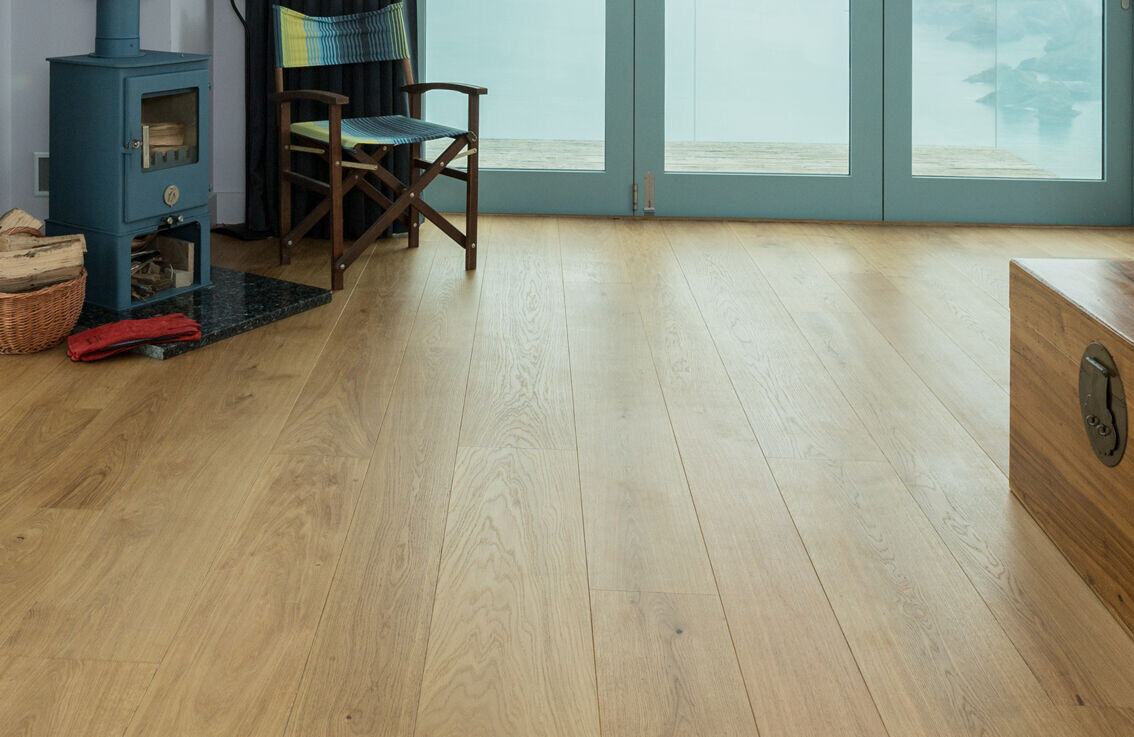
Cut from Baltic trees
WOODlife mainly uses logs from Baltic trees between 100 and 175 years old. Due to the Nordic climatic growth region, Baltic oak and ash grow slow and steadily. The oak timber is therefore considered to be amongst the best of what Europe has to offer: it’s very stable and dense, it’s consistent in color, has a calm appearance and is rich in tannins.
Complementary products
Besides floors, WOODlife also manufactures complementary products which can all be color matched to floor products:
- Matching stair elements: closed, open and floating treads, including hand railing, metal base constructions, glass panels, and more.
- Cladding for walls & ceiling: plank look, ribs (laths) and patterns.
- Windowsills
- Skirting
- Floor vents and duct grids
- and even decking
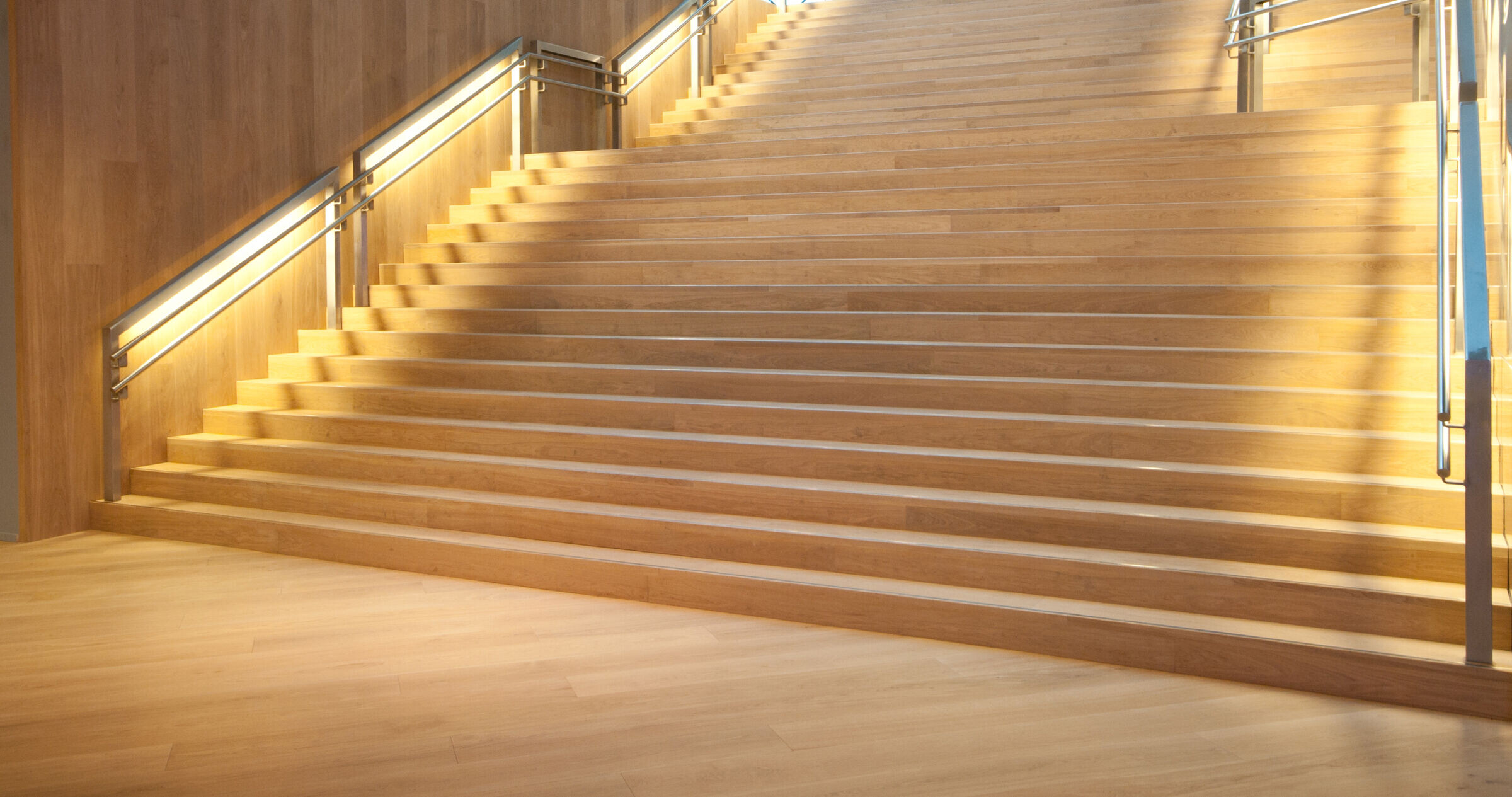
A Dutch-Lithuanian flooring company
WOODlife Flooring designs and manufactures high quality, engineered flooring and matching complementary products. WOODlife Flooring is a Dutch flooring brand with a Lithuania based production facility, which was established in 1993, not long after Lithuania’s independence. WOODlife's main sales office is located in the Netherlands.
WOODlife's Dutch founders, Thomas van Lieshout and Stefan Verhagen, met each other during their studies at a university for applied forest sciences in Germany. Their shared passion for forest products and design, and their strong friendship, led to the establishment of WOODlife in 2005. In 2008, they took over an existing floor factory near Marijampole, Lithuania.
Reference projects
Statoil regional and international offices
The structure in Norway by A-lab has five oblong building elements in a set-up inspired by the classic game of Mikado and is stacked side by side and on top of each other, with an airy, sunlit atrium at the center of this stack of giant pick-up sticks. The building is a bold example of creative use of prefabricated products and individualized standard components which makes a sensible contribution to future-oriented, environmentally friendly expressive architecture. The architects specified flooring, stair steps and cladding in European Oak with transparent white hardwax oiled finish from WOODlife.
This is a 4-story, split level house. The concrete slabs have a unique tapered edge detail which gives the house a slender profile. Expansive glazing maximizes the panoramic views and frames the sculptural pine trees that dot the nearby landscape. These pines are a reminder of the cool exterior climate, belied by the warmth created by the interior color palette and choice of materials. Solid European oak floorboards, timber battened ceilings and patinated metal give the interiors rich finishes. Not a single white plasterboard surface can be found in this home with mineral chalk paint softening harder surfaces of concrete and steel.
Natural woods were chosen as the main finishing material of the volume of this home as a reinterpretation of the Lithuanian traditional wooden house. The main characteristics of Lithuanian traditional houses are laconic volume, double pitched roof, wooden blinds, wooden finishing and granite rock foundations. Considering that the project site is in regional park territory, the idea was to remind one of the qualities of the traditional farmstead house in a contemporary way.